Many of the difficulties encountered by users during processing can be solved by Dawn Machinery
With years of accumulated experience, Dawn Machinery can create new processing solutions and machine configurations for customers from scratch within 6 months. We will refer to various conditions such as process, model selection, fixtures, tools, feed modes, etc., and make professional planning to create the highest production energy efficiency, whether it is turning, honing, high and low speed compound processing, and special-shaped grinding. , Gear grinding, eccentric grinding, end gear grinding, etc., can be assured to us.
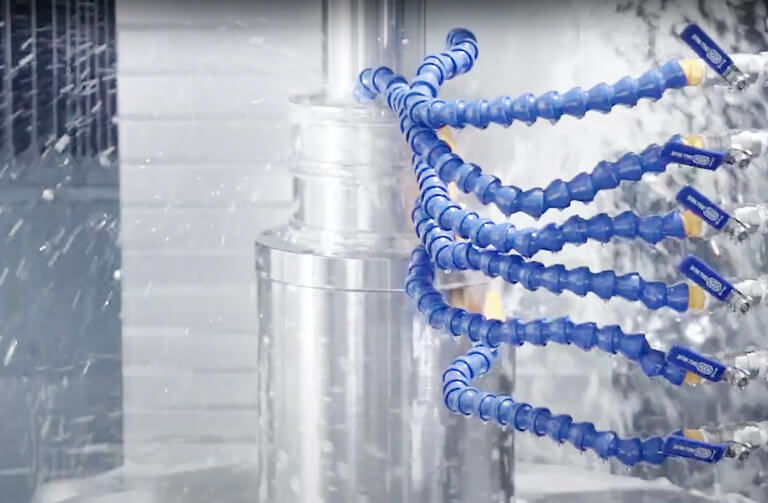
Offering Optimal Solutions On Spindle Sleeve Grinding
When engineers are planning the spindle sleeve grinding, they need to consider concentricity, roundness, and cylindricity accuracy. The quality of these three would definitely affect the following processing processes. As a result, machine model selection must meet the planned procedure, and after the model selection, they need to dedicate to the design of fixture equipment, since the planning of fixture devices would further affect material deformation, feeding and loading, repeated accuracy of clamping, and so on and so forth. Then, it is the processing productivity planning, which includes processing time, tools, tool feeding models.
Simply put, the design of vertical grinding and the turnkey solution we offer together help customers get rid of their reliance on experienced personnel who may hold certain know-how and are not willing to share. Our vertical processing of vertical spindle sleeve needs a simple setting only and with the support of dialogue-based HMI, users can get to our manufacturing tempo once they are shortly trained.
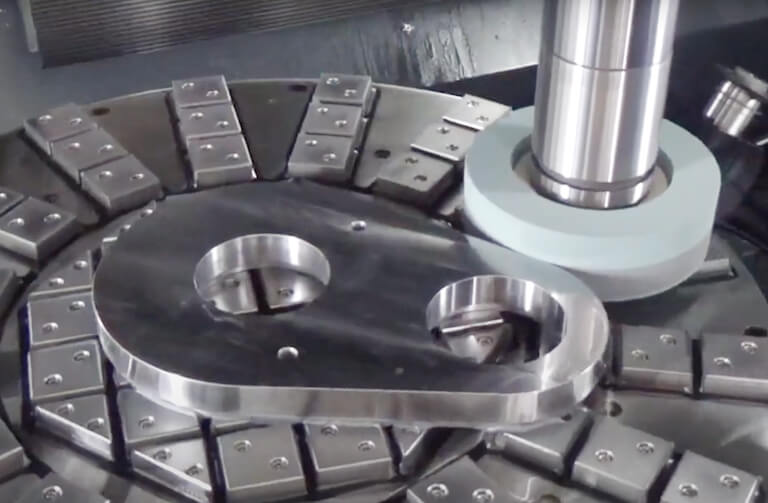
Complicated Profile Grinding Capacity
For the case of complicated profiles, the arrangement of the controller, machine, axial issue, rotational tables, and other technical issues are important. Regarding the transmission, there shall be no backlash so that the targeted profile could be achieved perfectly. As a result, we have prepared selections such as programs and tool feeding modes for our customers.
In sum, repeatability depends on the arrangement of the controller, no-backlash transmission, DD drive plus a hydrostatic table. The capacity to coordinate all this stuff is based on our profound experience. We know how to design the program and set the targeted accuracy, rendering the profile accuracy within 2 u.
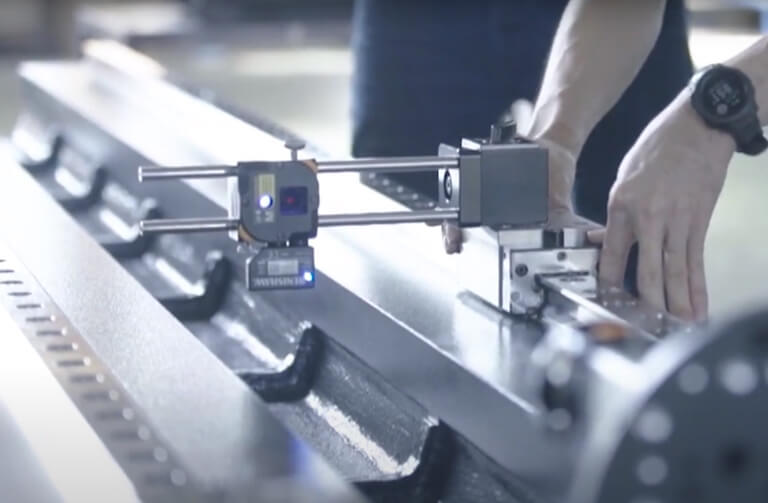
Control of Minimum Tolerance
For the control of grinding accuracy, the structural accuracy of a machine is the very basis. Besides this issue, there are also fixtures, grinding wheels, processing methods, and other related technical issues. These efforts all affect the accuracy of the finished products. Only with well-coordinated results, can the accuracy be controlled within 1 u. In regard to feeding, we are able to achieve 0.1 u micro feeding, because we have controlled many critical techniques.
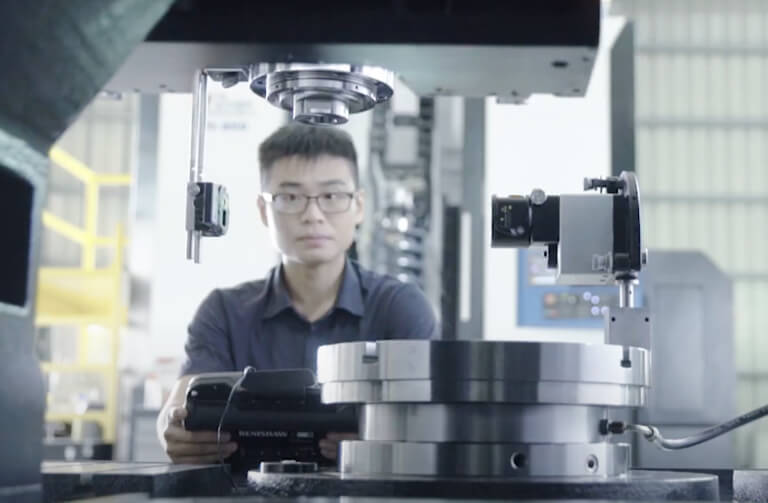
The Key That Ensures Machine Reliability
We have a rigidity structure that can ensure machine reliability. During the assembly process, we use laser devices for geometric inspection for accuracy. We also inspect transmission mechanism, rotational table, grinding wheel, etc. For customized inspections, we also are capable of doing what is requested by our customers.
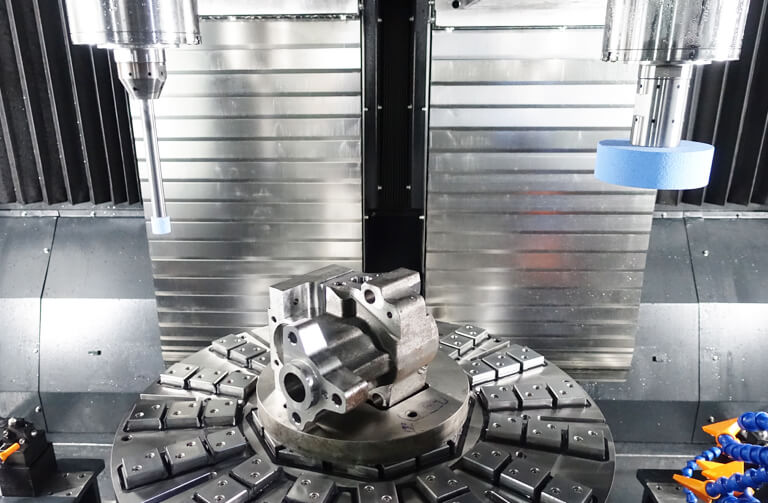
Structural Advantages of Our Vertical Grinders
Our grinder is designed with a double column structure, which contains five advantages
- There are four powerful roller linear guides on the X-axis
- High precision relocation accuracy of rotational table minimizes tolerances
- Cutting area and transmission area are separated so the transmission would not be affected by cutting chips and powders
- LCG machine tool structure ensures low processing altitude, achieving better accuracy
- Compatible with double spindle and single spindle mode as well as other customized processing modes
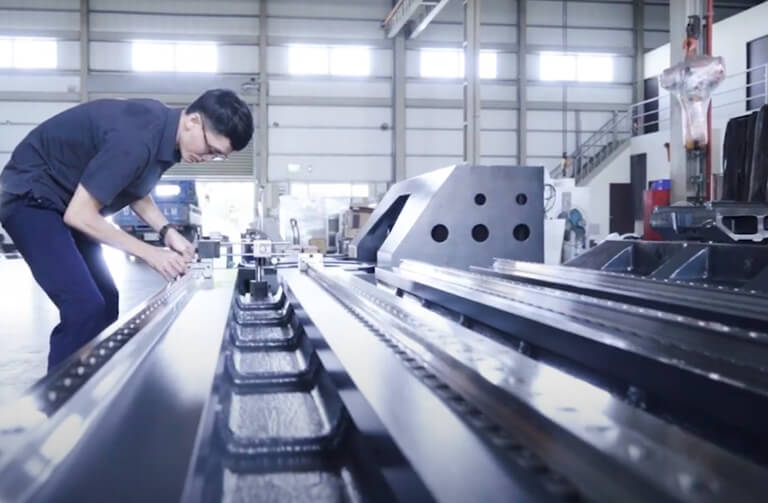
The Linear Guide Brands
We adopt linear guides made in Switzerland and rollers made in Germany, ensuring high assembly accuracy. The entire straight traverse is controlled within 1 u accuracy; X and Z axes are controlled within 2 u, and are both inspected by laser devices. Besides, axial accuracy is controlled within 3 u and the repeatability is controlled within 2 u. buyers can choose a linear motor, the none-screw backlash for synchronized X and C axes. If the work pieces are of complicated profiles, or the processing is of an eccentric circle, the profile accuracy can still be controlled within 2 u.
Famous Brands
- 90% of our critical components are famous brands from either foreign or domestic suppliers.
Spindle
- SETCO: 6000 hours under normal operation
- SKF: 6000 hours under normal operation
- THETA: 6000 hours under normal operation
Transmission System
- Switzerland linear guide : SCHNEERBERGER
- Ball supported bearing : NSK
- German Roller : REXROTH 50000 hours under proper maintenance
- Coupling KTR
Electric Component
- Relay (MYJ) : OMRON / 40 million times
- Relay (LY) : OMRON / 50 million times
- Relay (G2R) : OMRON / 10 million times
- Filter : SCHAFFNER / 320000 hours
- No fuse switch: FUJI / 20000 times
- Circuit Protector: SCHNEIDER / 20000 times
- Electromagnetic contactor : SCHNEIDER / 2000 times
- Overload Protector : SCHNEIDER
- Security Module : SCHNEIDER MTTFd > 243 years
- DC Power Supply Unit : ACRO / 60000 hours
- Pneumatic System : SMC
- Extensible Shield : 10000 hours
Contact Us
We aim to achieve the goal of high accuracy with our machine models
We are looking forward to hearing from you about your problems and are willing to offering our support. Please don’t hesitate if you need us.
Inquiry Form